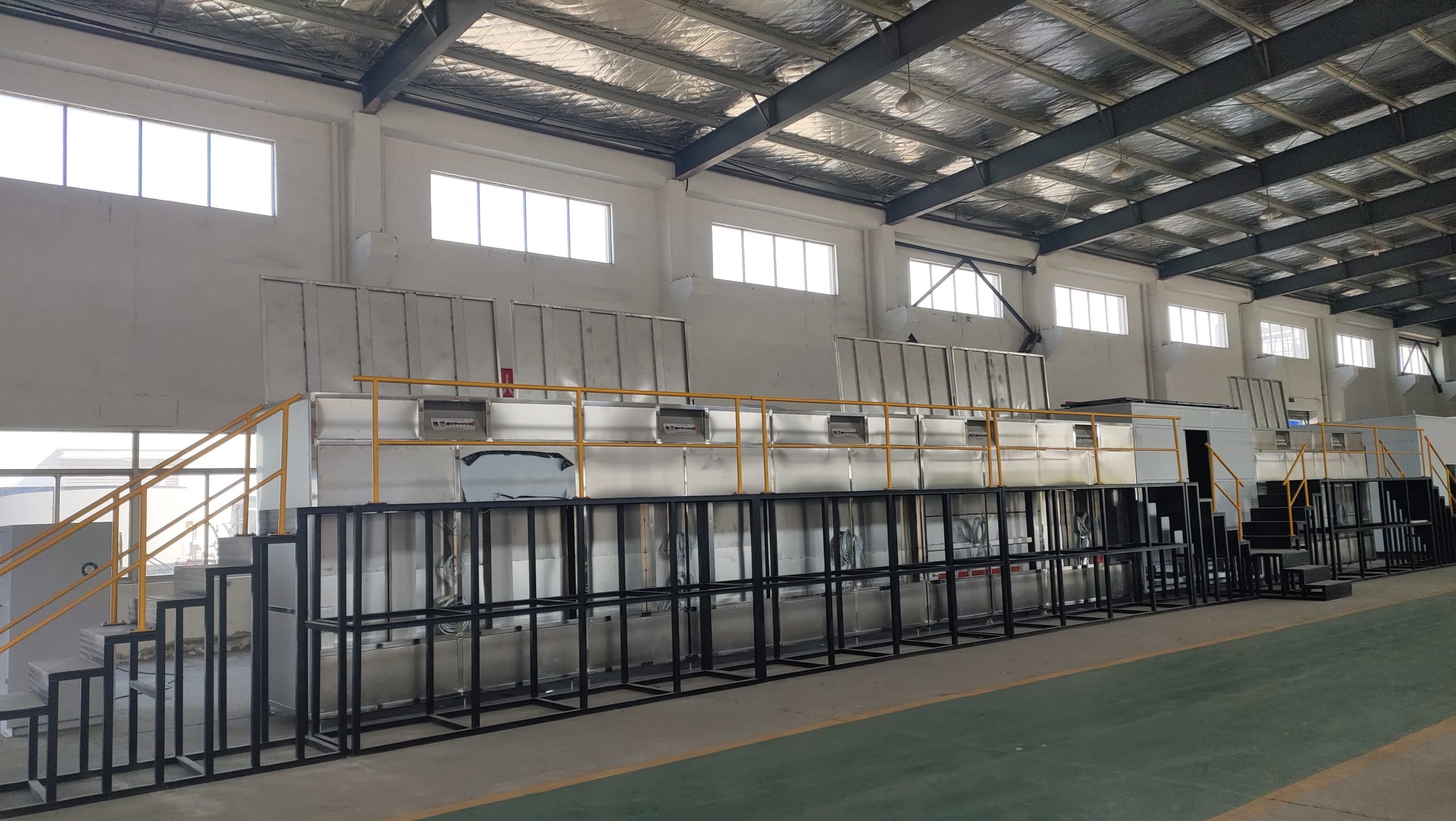
After allowing sufficient dwell time, excess surface penetrant is carefully removed. A developer is then applied, which draws the penetrant trapped in the defects back to the surface, making the flaws visible. Under UV light (fluorescent inspection) or white light (color contrast method), surface cracks and discontinuities appear as bright yellow-green fluorescence or red indications respectively. With the naked eye, inspectors can clearly observe the shape and distribution of surface defects.
FPI is one of the five conventional NDT techniques, alongside radiographic testing (RT), ultrasonic testing (UT), magnetic particle inspection (MPI), and eddy current testing (ECT). Due to its unique advantages, penetrant inspection is widely used across modern industries. It plays a crucial role in evaluating the integrity and continuity of engineering materials and components, supporting quality assurance, saving raw materials, optimizing manufacturing processes, and improving productivity. It is an indispensable part of both manufacturing and maintenance workflows.
🕰️ A Brief History of Penetrant Inspection
Penetrant testing is one of the earliest NDT methods, dating back to the early 20th century. Before advanced NDT methods emerged, experienced inspectors relied on visual signs like rust patterns on steel plates to detect potential cracks—since water entering cracks would cause localized corrosion over time.
The earliest formal penetrant method, known as the “oil and whiting” technique, involved applying a mixture of heavy oil and kerosene to the workpiece. After a short dwell time, the surface was wiped clean and coated with a mixture of alcohol and white chalk. As the alcohol evaporated, oil trapped in surface cracks seeped back and stained the white layer, revealing the defects. This simple technique gained widespread use across industries.
In the 1930s, magnetic particle inspection (MPI) became popular, particularly in railway maintenance, as it could detect both surface and near-surface defects—even through light contamination—and provided fast and clear results. Many predicted that penetrant inspection would become obsolete.
However, with the rapid development of the aviation industry and the increasing use of non-ferromagnetic materials like aluminum, titanium, and stainless steel, MPI was no longer sufficient. This renewed interest in penetrant inspection, prompting significant innovations.
To improve reliability, dyes were added to penetrants, followed by the introduction of fluorescent dyes and developer powders, allowing for high-sensitivity flaw detection under UV light. This marked a new era for penetrant testing.
Fracture mechanics research revealed that even micron-scale surface cracks can cause catastrophic failures under harsh conditions. As a result, developing high-sensitivity, non-toxic penetrant materials became a major research focus.
🌍 The Rise of Modern FPI Materials & Technology
In the 1960s–70s, international breakthroughs led to the development of smoke-free fluorescent penetrants, water-washable systems, and closed-loop inspection systems—which improved both environmental safety and detection sensitivity. Special low-halogen formulations were developed for use on nickel alloys, titanium, and austenitic stainless steel, ensuring material compatibility.
In China, early penetrant testing was based on Soviet formulations. By the mid-1960s, many domestic enterprises began independently developing dozens of penetrant types. In the late 1970s, China successfully created color contrast penetrants capable of detecting micron-wide cracks, followed by water-washable and post-emulsifiable fluorescent penetrants with performance on par with international brands. These innovations saw rapid adoption across the industrial sector.
🚀 Industry Growth & Future Prospects
With continued advancements in testing technology, both domestic and international companies have emerged, offering complete FPI material kits and automated systems, accelerating standardization and systemization.
Recent trends focus on:
-
Low-toxicity, high-sensitivity materials
-
Specialized penetrants for unique applications
-
Improved process efficiency and accuracy
-
Refining capillary-action theories for micro-defect detection
-
Enhancing standards and procedural control
As science and technology evolve, FPI remains a vital tool for quality assurance, particularly for components made from non-ferrous, non-magnetic materials. Its future promises even greater precision, efficiency, and environmental safety.
✅ Looking for FPI Solutions?
We specialize in customized fluorescent penetrant inspection (FPI) lines and equipment, designed for industries such as aerospace, automotive, shipbuilding, and petrochemical.
🔧 From compact test stations to full automated inspection lines🌐 We deliver NDT solutions that meet international standards.
📩 Contact us today to learn how our FPI equipment can enhance your quality control process.